
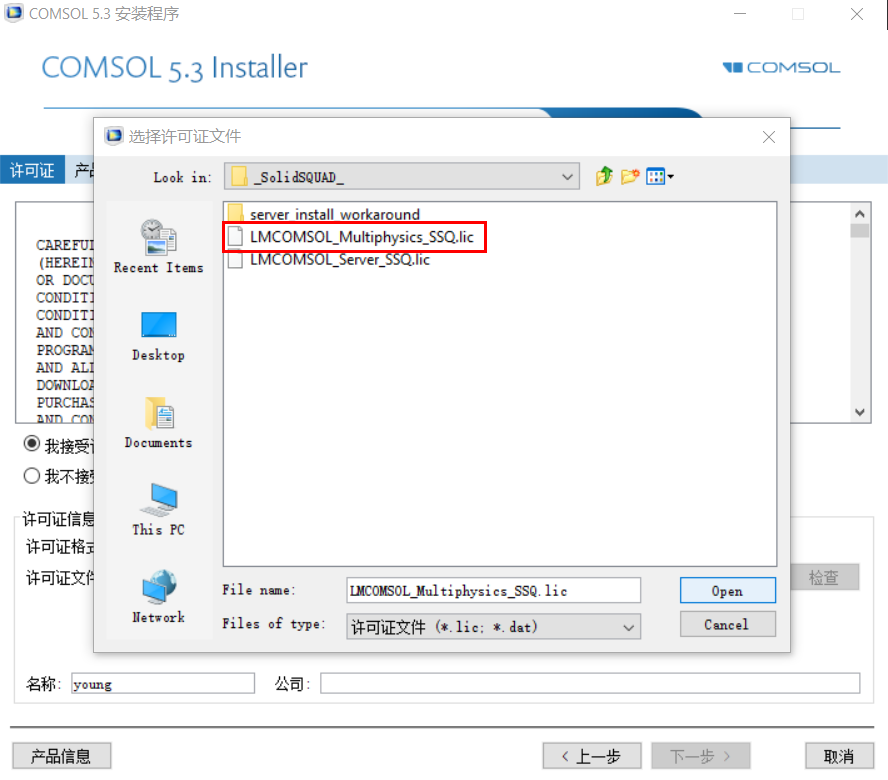
Wet chemical etching of the PSG layer is therefore avoided and a self-aligned metallisation process can be developed with electrochemical deposition techniques. Ablation of the SiN x coating and dopant diffusion are then performed simultaneously with a pulsed laser before metallisation.
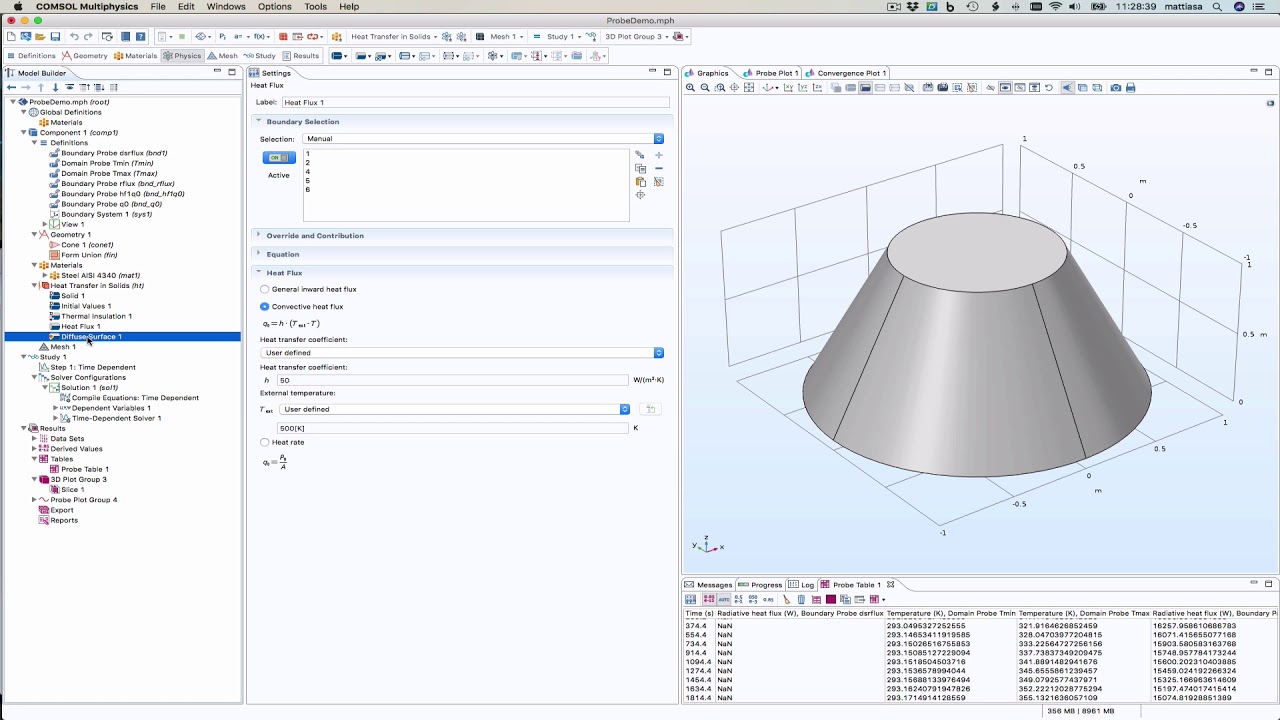
The resulting PSG layer is covered with silicon nitride (SiN x) for passivation and antireflection purposes. In this process, a homogenous emitter is formed by thermal diffusion of phosphorous.
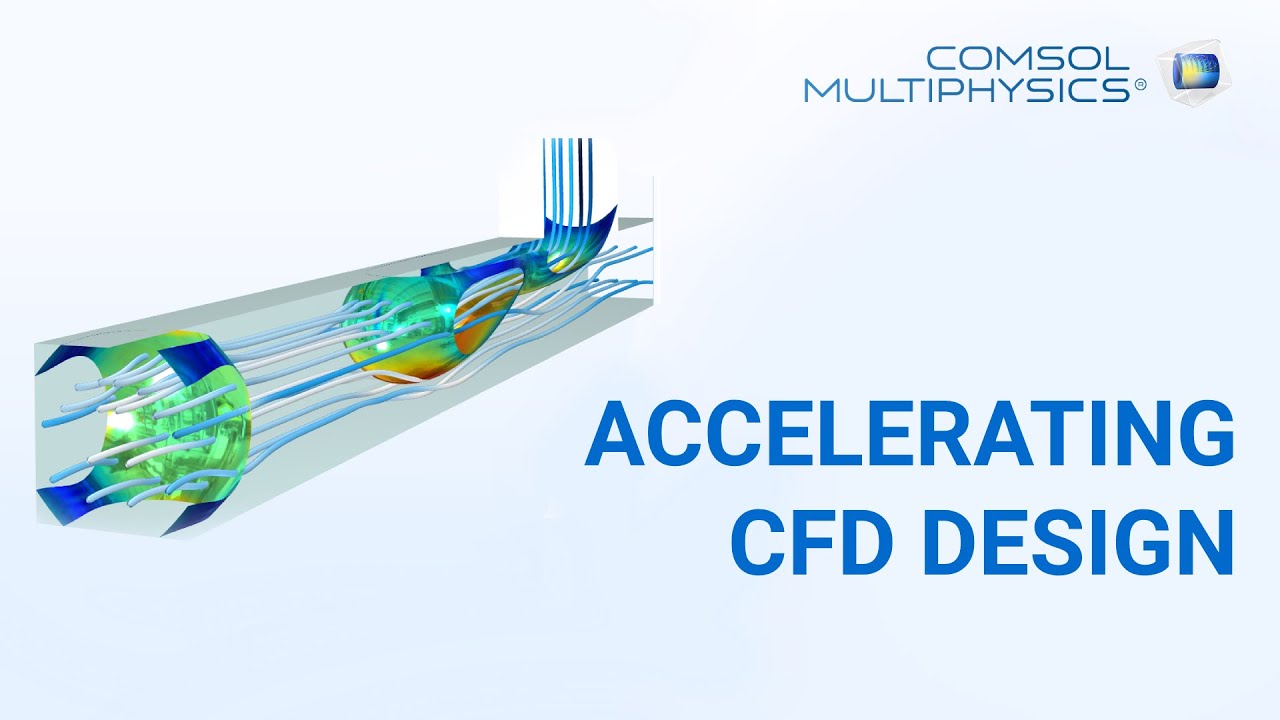
In the perspective of a complete self-aligned process, a reduced number of technological steps is proposed to form selective emitters on the front surface of p-type silicon wafers (Figure 1, Process B). Recent results have shown that around a 0.5% increase in solar cell efficiency could be obtained when using phosphosilicate glass (PSG) as a source of dopants to form highly doped areas on the emitter side according to Process A in Figure 1. In this context, laser processing provides a good opportunity to achieve such a structure with a minimum number of technological steps and without alignment when coupled with front side electrochemical metallisation. Selective emitter technology can provide a significant increase in solar cell efficiency, but today most of the approaches need many processing steps and alignment procedure.
